Stepper motors are a type of synchronous motor widely used for precise control of position and speed in various applications. The unique characteristics of stepper motors allow them to move in discrete steps, making them ideal for applications that require precise control of motion. This article delves into the analysis of stepper motor velocity, examining the factors that influence it, methods of control, and its implications in various applications.
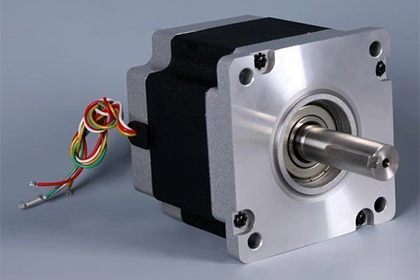
Understanding Stepper Motor Basics
A stepper motor operates by moving in discrete steps, with each step corresponding to a specific angle of rotation. The stepper motor's ability to move incrementally allows for precise control of angular position without the need for feedback systems, which are typically required in other types of motors. Stepper motors are classified into various types, including permanent magnet, variable reluctance, and hybrid stepper motors, each with its own operating principles and characteristics.
Velocity Limitations of Stepper Motors
The velocity capabilities of stepper motors are influenced by several factors, including motor design, drive electronics, and the load applied to the motor. Achieving high velocities with stepper motors requires careful consideration of these factors. Next, we will take Lunyee's stepper motor worm gearbox driver kit as an example.
- Motor Design: The design of the stepper motor affects its maximum achievable velocity. Factors such as rotor inertia, winding inductance, and motor size play a role in determining the motor's velocity capabilities. Higher inertia or larger motor sizes may limit the maximum speed that can be attained due to increased mechanical inertia and electrical time constants.
- Drive Electronics: The drive electronics used to control stepper motors also impact their velocity capabilities. Stepper motor drivers provide the necessary current and voltage to the motor windings, enabling precise control of the motor's motion. The speed and performance of the drive electronics, including the pulse frequency and control algorithms, influence the maximum achievable velocity. Advanced microstepping techniques can increase the resolution and smoothness of motor motion but may reduce the maximum speed due to the increased number of steps required for a complete revolution.
- Load Considerations: The load applied to a stepper motor plays a crucial role in determining its maximum achievable velocity. The motor's torque output decreases as the speed increases, which can limit the motor's ability to accelerate or maintain high velocities. It is essential to consider the torque-speed characteristics of the motor and ensure that the load does not exceed the motor's capabilities.
Maximum Speed and Frequency
The maximum speed and frequency of a stepper motor depend on various factors, including the motor's step angle, the drive electronics, and the control methodology employed.
- Step Angle: The step angle refers to the angular displacement produced by each step of the motor. Common step angles for stepper motors include 1.8 degrees (commonly known as full step) and 0.9 degrees (half step). Smaller step angles, such as 0.45 degrees or microstepping, can provide higher resolution but may result in reduced torque and speed capabilities. The maximum speed of a stepper motor is typically inversely proportional to its step angle. Smaller step angles allow for finer motion control but may limit the maximum speed due to the increased number of steps required for a complete revolution.
- Drive Electronics and Control Methodology: The drive electronics and control methodology employed significantly impact the maximum speed and frequency of a stepper motor. The pulse frequency, or the rate at which electrical pulses are applied to the motor, directly affects the motor's rotational speed. Higher pulse frequencies enable faster motor speeds, provided that the motor and the drive electronics can handle the increased frequency. The control methodology used, such as full-step, half-step, or microstepping, affects the motor's smoothness of motion and resolution but may reduce the maximum speed due to the increased number of steps required for a complete revolution.
Advancements in Stepper Motor Technology
Advancements in stepper motor technology have led to improved velocity capabilities and enhanced performance. Manufacturers have developed innovative techniques to overcome the limitations of traditional stepper motors and achieve higher speeds and smoother motion control.
- Hybrid Stepper Motors: Hybrid stepper motors combine the benefits of permanent magnet (PM) and variable reluctance (VR) stepper motor technologies. By integrating these technologies, hybrid stepper motors can achieve higher torque and speed capabilities compared to traditional stepper motors. This makes them suitable for applications that require high-speed and high-precision motion control.
- Closed-Loop Control: Closed-loop control systems, utilizing position feedback devices such as encoders or resolvers, enable more precise control and enhanced velocity capabilities for stepper motors. By continuously monitoring the motor's position and adjusting the control signals accordingly, closed-loop control systems can compensate for errors and improve the motor's speed and accuracy.
Practical Applications and Implications
The precise control of velocity in stepper motors makes them suitable for a wide range of applications across various industries. Some notable examples include:
- CNC Machinery: Computer Numerical Control (CNC) machines use stepper motors for precise control of cutting tools and workpieces. The ability to accurately control position and velocity is essential for producing high-quality parts with tight tolerances.
- Robotics: In robotics, stepper motors are used for joint actuation and precise control of movement. Their ability to move in discrete steps ensures accurate positioning, which is crucial for tasks such as pick-and-place operations and robotic surgery.
- 3D Printing: Stepper motors are widely used in 3D printers to control the movement of the print head and build platform. The precise control of velocity and position enables the creation of detailed and accurate 3D objects.
- Industrial Automation: Stepper motors are employed in various industrial automation applications, including conveyor systems, packaging machines, and assembly lines. Their reliability and precision make them ideal for tasks requiring consistent and repeatable motion.
- Medical Devices: In the medical field, stepper motors are used in devices such as infusion pumps, diagnostic equipment, and surgical instruments. The precise control of velocity and position ensures accurate dosing and reliable operation.
Conclusion
Stepper motors offer precise positioning and control capabilities for various applications. Understanding the velocity characteristics of stepper motors is crucial for optimizing their performance and achieving accurate motion control. Factors such as motor design, drive electronics, and load considerations influence the maximum achievable speed and frequency of stepper motors. Advancements in stepper motor technology, such as hybrid stepper motors and closed-loop control systems, have further improved their velocity capabilities. By considering these factors and advancements, you can select and configure stepper motors to meet the specific requirements of their applications, ensuring reliable and efficient motion control.